Reliable Ammonia Catalyst Solution
Refinery
SYAMCAT's secondary steam reforming catalyst is a type of nickel catalyst specifically engineered for high-temperature secondary reforming furnace or autothermal furnace steam reforming processes. It provides excellent activity, heat resistance, and structural stability.
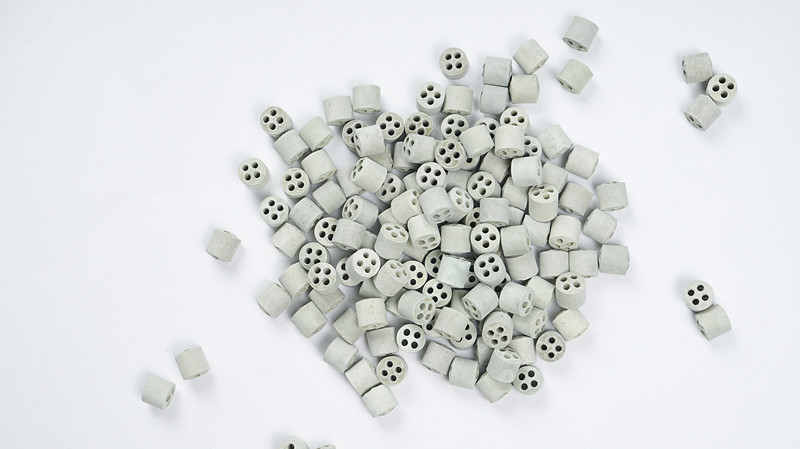
Why Choose SYAMCAT Secondary Steam Reforming Catalyst?
≥10%
More than 10% active components Nickel Oxide (NiO) are added
≥2%
The K2O content is more than 2%, with good anti-carbon performance.
5+
5+ years of high guaranteed service life
Production Process of SYAMCAT Secondary Steam Reforming Catalyst
① Active Component Preparation: Begin by dissolving nickel nitrate, the active component, to ensure optimal temperature resistance and stability.
② Incorporating High-Temperature Stability: Recognizing the need for stability at high temperatures (1300-1400℃), this catalyst is engineered not to fuse or deform.
③ Precipitation Method: Utilize the precipitation method to create the catalyst, involving the addition of α-Al2O3 powder to the nickel nitrate solution.
② Incorporating High-Temperature Stability: Recognizing the need for stability at high temperatures (1300-1400℃), this catalyst is engineered not to fuse or deform.
③ Precipitation Method: Utilize the precipitation method to create the catalyst, involving the addition of α-Al2O3 powder to the nickel nitrate solution.
④ Neutralization and Precipitation: Achieve the desired catalyst properties by neutralizing the mixture with potassium carbonate, then precipitating it to form the base catalyst.
⑤ Drying and Roasting: The catalyst base is then carefully dried and roasted to achieve the desired properties.
⑥ Addition of Stabilizers: To enhance stability, add calcium aluminate cement and graphite, ensuring the catalyst's structural integrity.
⑦ Mixing, Kneading, and Molding: Carefully mix, knead, and mold the catalyst material to the desired shape for uniform performance.
⑤ Drying and Roasting: The catalyst base is then carefully dried and roasted to achieve the desired properties.
⑥ Addition of Stabilizers: To enhance stability, add calcium aluminate cement and graphite, ensuring the catalyst's structural integrity.
⑦ Mixing, Kneading, and Molding: Carefully mix, knead, and mold the catalyst material to the desired shape for uniform performance.
⑧ Final Drying: The shaped catalyst is dried to perfection, resulting in the finished product, ready for use in the demanding environment of secondary steam reforming.
Sencondary steam reforming catalyst production process flow chart:
Mixing →Neutralization→Precipitation →Drying→ Roasting →Kneading→Molding→Drying
SYAMCAT Ammonia Secondary Steam Reforming Catalyst Solution
In hydrocarbon steam reforming to ammonia and methanol syngas plants, the purpose of the secondary steam reforming is to further reform the residual methane of the primary reforming gas to meet the syngas requirements. The secondary conversion is the worst working condition equipment, the catalyst in the conversion furnace for a long time in the high temperature and high pressure conditions.
At the top of the secondary steam reforming furnace, the temperature of the oxygen (air) mixed with the primary steam reforming gas is about 1260°C. If there is any problem with the mixer or the airflow distribution is not uniform, the local maximum temperature can be up to 1980°C. The catalyst in the secondary steam reforming furnace is under such high temperature and pressure conditions. The catalyst of the secondary steam reforming is equivalent to being sintered under such working conditions, and the pore structure, specific surface and other physical properties of the catalyst may undergo large changes, which will have a greater impact on the performance of the catalyst, especially the activity.
5 results
ViewShowcase
ZnO Desulfuration Catalyst has deep desulfurization extent, easy to use and high sulfur capacity.
Hydrogenation catalyst for hydrogen production with cobalt molybdenum nickel ternary active components.
SYAMCAT B317 is an energy efficient catalyst made by precipitation process.
Secondary steam reforming catalyst has good activity, heat resistance, and structural stability.
Pre-reforming catalyst is a high Ni system supported on a porous carrier.
SYAMCAT's Technology Service of Secondary Steam Reforming Catalyst

Customized Catalyst Solutions:
The professional technical team will optimize the synthesis ammonia catalyst according to your operating conditions/requests and propose the most suitable product to you;

Guaranteed 5-Year Service Life:
An official authoritative guarantee of a service life of at least 5 years

Expert Remote Guidance and Technical Support:
Remote guidance and technical services for catalyst start-up, loading, maintenance of any in-service shutdown, etc. If on-site instruction is required, a small fee will be charged according to the time;

Real-Time Production Monitoring and Support:
Monitor and record data for your production operations at any time (your cooperation is required), and provide real-time technical advice or parameter adjustments if necessary for various conditions during operation.
FAQs of SYAMCAT Secondary Steam Reforming Catalyst
- Q:
- How many years is the service life of your secondary steam reforming catalyst?
- A:
- Q:
- What is the inlet temperature to the nickel catalyst bed?
- A:
- There is a great influence of temperature on the reduction process. No matter it is considered from nickel reduction equilibrium, or ammonia cracking equilibrium, or the reaction rate, it is always beneficial to raise temperature. In the whole reduction period, the inlet temperature of the nickel catalyst bed should be kept as high as possible, generally, in the range of 450-650℃.
Please send your message to us
SYAMCAT is a professional manufacturer of synthetic ammonia catalysts with over 30 years of catalyst experience and history,Through continuous technological innovation, we offer catalyst solutions for ammonia production.If you would like to learn more or are in search of a manufacturer for synthetic ammonia catalysts for your company, please feel free to contact us.
- Tel
- *Title
- *Content
subscription